Raphael Küff: Herausforderungen eines Produktionsleiters
- Stephan Bellmann
- 23. Jan.
- 23 Min. Lesezeit
Aktualisiert: vor 4 Tagen
Über die Aufgaben eines Produktionsleiters bei Saint-Gobain Sekurit, die täglichen Herausforderungen und Industrie 4.0 Ansätze.
Inhalt
Über das Interview
Das Interview mit Raphael war sehr interessant. Man merkt schnell, dass Raphael in seinem Element ist, wenn es um das Thema Produktion geht. Raphael erzählt aus seinen langjährigen Erfahrungen und vor allem von seinem Weg vom Assistenten bis zum Produktions- und Werksleiter. Man kann sehr gut in seine Geschichten eintauchen. Sehr schnell bekommt man einen guten Eindruck über den Alltag eines Produktionsleiters, über dessen Verantwortungen und Herausforderungen. Welche Probleme erschweren die tägliche Produktion? Welche Optimierungspotenziale können diesen Problemen entgegenwirken? Welche Rolle spielen Industrie 4.0 Technologien dabei? Und wie wichtig sind Erfahrungen im Business der Beratung?
"... es stand vorher immer im Raum, dass wenn wir den Kunden zu einem Bandstopp zwingen, weil wir keine Windschutzscheiben liefern, dass man uns dafür pro Stunde einen extrem hohen Betrag in Rechnung stellen würde."
Über Raphael Küff
Raphael war Produktions- und Werksleiter bei Saint-Gobain und bringt dabei über 14 Jahre Erfahrung aus diesem Bereich mit. Zudem ist er danach aus der direkten Produktion in die Beratung gewechselt. Ein Perspektivwechsel, der ihm tiefere Einblicke in die jüngsten Technologien rund um das Thema Industrie 4.0 gegeben hat.
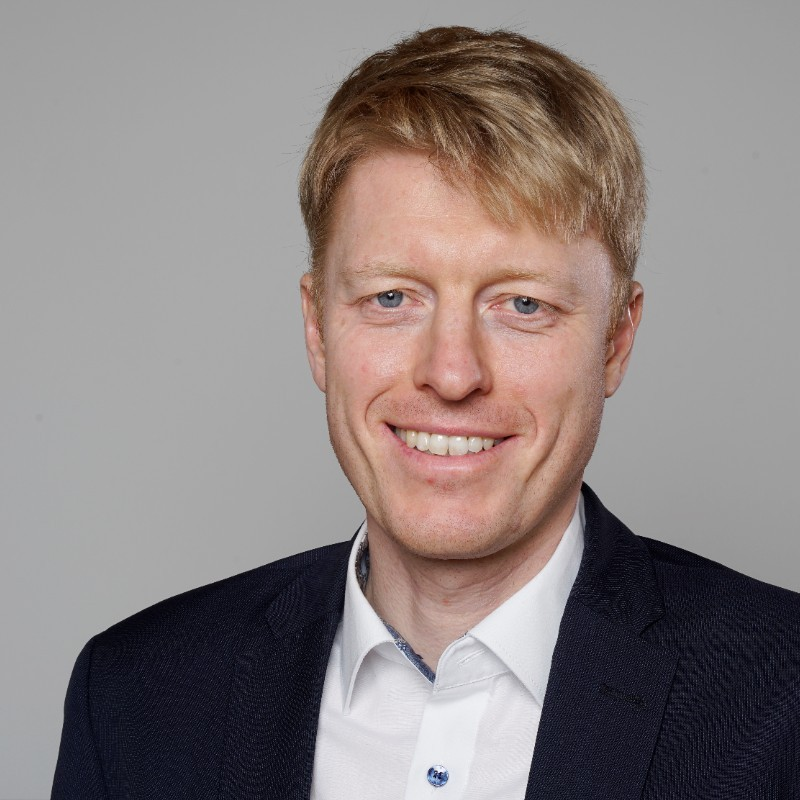
Hauptthemen
Verantwortung eines Produktionsleiters und seine Produktion

Es geht zum einen über die Verantwortung eines Produktionsleiters. Zu den Verantwortungen gehören im Besonderen die Ausbringungszahl, die Verluste, das OEE und die Arbeitssicherheit. Mit welchen Herausforderungen Raphael im Alltag als Produktionsleiter umgehen muss, erläutert er am Beispiel der Fehlersuche von Luftbläschen im Laminat in der Produktion von Windschutzscheiben (Interview). Das Problem ist, dass dieser Fehler erst am Ende der Produktionslinie erkannt wird. Wurde dieser Fehler tatsächlich erkannt, beginnt die Fehlersuche. Als Produktionsleiter muss er entscheiden, ob die Produktion gestoppt werden muss oder nicht. Ein Stopp hätte enorme Folgen für die Belieferung der Kunden. Zudem: wie soll mit der fehlerhaften Produktion umgegangen werden? Gibt es genug Personal, um die fehlerhafte Produktion nacharbeiten zu können? Gibt es Engpässe bezüglich der Transport- und Lagergestelle? Gibt es als Folge eine Unterversorgung gegenüber dem Kunden? Und können die Lagerbestände weiterhin abgedeckt werden? All diese Abhängigkeiten müssen vom Produktionsleiter entschieden und gemanagt werden.
In der Produktionslinie der Windschutzscheiben wird das Floatglas zunächst in einer Linienproduktion getaktet laminiert (Interview). Danach werden die laminierten Windschutzscheiben in Batches autoklaviert. Und am Ende werden Restarbeiten, Säuberungen und Kontrollen durchgeführt.
Zum näheren Produktumfeld gehören Seitenscheiben (Interview) und Windschutzscheiben (Interview) eines Autos, die als Produkte unterschiedliche Anforderungen erfüllen müssen und somit einen direkten Einfluss auf die Produktion haben.
Corona: Radikaler Umschwung der Produktion

Zum Start zur Corona-Pandemie sind viele Kunden (VW, BMW usw.) in Kurzarbeit gewechselt. Dadurch musste auch die Produktion von Sekurit innerhalb von 24 Stunden gestoppt und die Mitarbeiter in Kurzarbeit geschickt werden. Ein Prozess, der zuvor undenkbar gewesen wäre, da der Ausfall der Produktion sehr viel Geld gekostet hätte. Sekurit hat sich dann entschieden, einen geplanten Umzug einer Produktionslinie vorzuziehen, sodass durch eine gewisse Menge an Vorproduktion erst der Abbau und dann der Aufbau ermöglicht werden konnte. In laufender Produktion wäre das nicht denkbar gewesen (Interview).
Von der Praxis in die Beratung

In Folge der Pandemie ist Raphael zu Umlaut gewechselt. Dort konnte er sich in die Thematik Industrie 4.0 vertiefen. Dabei war er verantwortlich für das Design von MES, SCADA, IT-Architekturen, OPC UA Standards und die Automatisierungspyramide (Interview). Seine praktischen Erfahrungen aus seiner Zeit als Produktionsleiter haben ihm dabei sehr geholfen. Diese helfen zwar in der Beratung, sind seiner Meinung nach aber nicht zwingend notwendig (Interview). Die Entwicklung zu Industrie 4.0 ist wichtig für die Zukunft, um zum einen beispielsweise gegenüber Rumänien oder China konkurrenzfähig zu bleiben und zum Anderen, um dem Fachkräftemangel entgegenzuwirken. Produktionen sind sehr unterschiedlich und daher kann der Begriff Industrie 4.0 nicht generalisiert für alle Produktionen verwendet werden. Dennoch kann es zu Optimierungen der Produktion beispielsweise über Machine Learning beitragen (Interview).

Interview
Du hast Elektrotechnik an der FH studiert, richtig?
Ja, ich habe betriebswirtschaftliche Elektrotechnik an der FH Aachen und der Hogeschool Zuyd in Heerlen studiert. Der überwiegende Teil fand an der FH in Aachen statt, aber wir hatten auch ein Semester in den Niederlanden an der Hogeschool Zuyd und ein Praxissemester in einem niederländischen Unternehmen. Zudem musste die Diplomarbeit in den Niederlanden oder im englischsprachigen Ausland geschrieben werden. Das habe ich in einem Labor an der Arkansas State University in den USA getan.
Hast du Niederländisch gelernt?
Ja, ein bisschen. Ich finde Niederländisch ist eine interessante Sprache. Es ist relativ einfach für uns, die Sprache zu lernen.
Und du sprichst Französisch!?
Ja, ich kann mich mit einem Franzosen unterhalten. Wenn aber jetzt Franzosen untereinander sprechen, dann schnappe ich einiges auf, aber ich kann nicht komplett folgen.
Was hast du nach deinem Studium gemacht?
Nach dem Studium habe ich ein Traineeprogramm bei Saint-Gobain gemacht. Saint-Gobain ist ja recht groß. Also die machen ganz viele Sachen. Isover stellt zum Beispiel Dämmung aus Glaswolle her, Rigips stellt Gipskartonplatten für den Trockenbau her, Weber und Maxit stellen Mörtel zum Verputzen her. Aber auch Bauglas und Autoglas werden von Saint-Gobain Unternehmen produziert und vertrieben. Bei dem Traineeprogramm war ich zuerst bei Pont-à-Mousson (Saint-Gobain PAM). Die produzieren Tiefbauarmaturen und Rohre aus duktilem Gusseisen. Also Entwässerungsrohre, Abwasserrohre, auch Trinkwasserrohre, aber eher für schwierige Gelände, die sehr stabil sein müssen. Auch Kanaldeckel machen die. Dann war ich noch innerhalb des Traineeprogramms ein halbes Jahr in den USA, im Forschungszentrum in Massachusetts. Da wurde zu diesem Zeitpunkt an einer Brennstoffzelle geforscht. Leider habe ich nicht in der Forschung mitgemacht, sondern Business Development gemacht. Also meine Aufgabe war es, Quellen zu finden, um die Forschung an der Brennstoffzelle mit zu finanzieren.
Da ging es zum Beispiel um den Bedarf an Wärme und Strom gleichzeitig. Also um dezentrale Kraft-Wärme-Kopplung.
Zuletzt war ich ein halbes Jahr bei Raab Karcher, das ist ein Baustoff-Fachhandel. Das gehörte damals noch Saint-Gobain. Dort war ich im Controlling. Danach wusste ich, dass ich weder im Baustoff-Fachhandel, noch im Controlling landen möchte.
So und dann war das Traineeprogramm vorbei. Was kam dann?
Dann ging es darum, was die erste Position innerhalb von Saint-Gobain nach dem Trainee-Programm sein wird. Eine Option war Saint-Gobain Oberland. Die heißen heute Verallia und gehörten damals noch zu Saint-Gobain. Da ging es um die Herstellung von Behälterglas. Nutellagläser, Parfumgläser, Bierflaschen, Wasserflaschen ... Da hätte ich in die Instandhaltung reingehen können. Das war technisch super interessant. Aber der Standort war so abgelegen, ich glaube der Ort hieß auch Oberland. Ich weiß es aber nicht mehr genau. Jedenfalls musstest du mit dem ICE bis nach Ulm fahren, dann mit dem Regionalzug bis zur Endstation. Und dann musstest du noch mal eine Dreiviertelstunde mit dem Taxi fahren. Dann kam relativ plötzlich die Anfrage von Sekurit. Sekurit macht Autoglas. Bei denen wurden zwei Projektteams zu einer Abteilung zusammengefasst, die ich dann leiten durfte. Die beiden Projekte waren auf mehrere Jahre angelegt. Das Sekurit Werk liegt direkt bei mir zu Hause in Herzogenrath, das war ein glücklicher Zufall. Und so sind wir dann eben nach Aachen bzw. Herzogenrath zurückgekommen.
Was für ein Projekt hast du bei Sekurit in Herzogenrath verfolgt?
Das eine Projekt war eigentlich so ein Vorläufer von Industrie 4.0, bzw. es hatte Komponenten davon. Aber damals gab es meines Wissens den Begriff Industrie 4.0 noch gar nicht. Das Projekt hatte ganz konkret die Aufgabe, alle wichtigen Prozessparameter kontinuierlich zu erfassen, statistisch auszuwerten und den Bediener zu alarmieren, wenn der Prozess sich verändert.
Man hatte schon vorher, also bevor ich in das Projekt eingestiegen bin, sämtliche Produktionsparameter aufgelistet. Zum Beispiel Glastemperaturen an diversen Stellen, Geschwindigkeiten von Transportbändern, Durchflussmengen von Kühlflüssigkeiten, alles mögliche. Man hat dann mit dem Produktionsteam analysiert, welche die wichtigsten Parameter sind und hat dann bei diesen geprüft, ob die Parameterwerte nicht bereits in irgendwelchen Steuerungen erfasst werden. Wenn ja, haben wir die Werte über OPC ins Netzwerk kopiert, wo wir sie mit einer Software für statistische Prozesskontrolle überwacht haben. Die grundsätzliche Idee dabei ist, dem Werker mitzuteilen, dass sich der Prozess verändert, bevor er sich außerhalb der Toleranz bewegt. Da haben wir uns über die Firma Q-Das Hilfe bezüglich statistischer Qualitätskontrolle geholt. Es gibt verschiedene statistische Verfahren, mit denen du anhand der gemessenen Prozessparameterwerte ermitteln kannst, ob der Prozess normal schwankt oder ob er sich verändert. Ein ganz einfaches Beispiel ist, wenn du einen Parameter hast, der eine normale Schwankung um einen Mittelwert hat. Dann ist ja die Wahrscheinlichkeit, dass ein Wert oberhalb oder unterhalb dieses Mittelwertes liegt, 50 %. Die Wahrscheinlichkeit, dass zwei aufeinander folgende Werte unterhalb des Mittelwertes liegen, ist nur noch 25 %. Die Wahrscheinlichkeit, dass es drei nacheinander sind, ist 12,5 % usw. Wenn du jetzt sechs oder sieben aufeinander folgende Werte unterhalb des Mittelwerts hast, dann hast du eine Wahrscheinlichkeit von 99,9 %, dass der Prozess nicht mehr zufällig schwankt, sondern sich verändert hat. Dann hätte es einen Alarm ausgelöst. Wir haben eine Darstellung der ganzen Produktionslinie auf einem großen Bildschirm dargestellt. Und wenn irgendwo ein Parameter einen Alarm ausgelöst hat, wurde der entsprechende Prozessbereich rot dargestellt. Da konntest du dann draufklicken und hattest diesen Hauptprozess noch mal feiner gegliedert. Der Unterprozess war auch rot und du konntest dich so bis zum Parameter selber durchklicken.
Wie gesagt, haben wir zum einen geprüft, welche von diesen Parametern schon in den Steuerungen erfasst wurden. Wir, also die SPS Programmierer in unserem Team, haben dann den entsprechenden Baustein aus dem SPS Programm kopiert und per OPC aus der Operations Technologie auf normale Rechner, also ins IT Netzwerk überführt.
Bei wichtigen Parametern, die nicht bereits in den vorhandenen Steuerungen eingebunden waren, haben wir nach günstiger Sensorik gesucht und diese über einfache Steuerungen und OPC ausgelesen.
Wenn beides nicht umsetzbar war, weil es zu teuer war oder weil es einfach technisch nicht ging, musste der Mitarbeiter selber die Parameterwerte erfassen. Dafür hatten wir noch eine separate Datenbank entworfen bzw. entwickeln lassen, in die der Mitarbeiter dann eben die Parameter zu einem gewissen Zeitpunkt händisch eintragen sollte. Und all diese Parameter, bzw. die erfassten Werte sollten in der Analysesoftware überwacht werden. Wenn sich irgendwas im Prozess außergewöhnlich ändert, dann sollte die Warnung kommen.
Als dann Ende 2008 die Lehman Brothers Pleite kam und damit verbunden die Weltfinanzkrise, wurde Cash die wichtigste Kennzahl im Konzern und alle Ausgaben, die nicht direkt zum Aufrechterhalten der Produktion nötig waren, wurden gestoppt. Und leider wurde auch mein Projekt eingestellt.
Sekurit hatte damals um Aachen herum drei Werke. Herzogenrath, Würselen und Stolberg. In Herzogenrath wurde nur Einscheibensicherheitsglas hergestellt, also Rückwand- und Seitenscheiben. Stolberg hat laminiertes Glas gemacht, also Windschutzscheiben. Und in Würselen war die Komplettierung. Das heißt, in Würselen waren in erster Linie Roboter für die Extrusion von Dichtlippen, Verklebung, etc.. Es gab einen Werkleiter für die Werke Würselen und Stolberg gemeinsam. Und der suchte einen Assistenten. So bin ich Assistent der Werkleitung geworden und wurde in der Position direkt zum WCM Black Belt ausgebildet. WCM steht für World Class Manufacturing. Das ist so ähnlich wie Six Sigma, wobei Six Sigma meines Wissens einen etwas wissenschaftlicheren Ansatz hat. WCM ist in erster Linie Lean Management.
Was beinhaltete das WCM bzw. was genau hast du da gemacht?
Man hat das eigentlich nicht gut gemacht aus meiner Sicht. Man hat von Konzernseite gesagt, wir machen jetzt WCM und hat das alles über Leute wie mich, also Assistenten und Stabsstellen, in die Werke gebracht. Jetzt war es bei mir beispielsweise so: Wir sind geschult worden und das war sehr umfangreich. Das heißt, wir hatten jeweils eine Woche Schulung, dann acht Wochen Umsetzung eines Projektes und dann musste man zu diesem Projekt auch ganz genau berichten. Man musste nachweisen, dass man die entsprechenden Einsparungen erzielt hat usw. Wenn man den theoretischen Test bestanden hat und das Projekt die Anforderungen an Methodik und Einsparung erfüllt hat, bekam man den Green Belt für die entsprechende Säule, zum Beispiel Qualität und Prozesskontrolle. Mit vier Green-Belts wurde man dann zum Black-Belt. Als ich dann zum Werkleiter gegangen bin und gesagt habe: Ja, also pass auf, die fordern jetzt, dass wir über die nächsten Jahre das, das, das und das umsetzen, meinte er zu mir: “Nehmen Sie es nicht so ernst. Wir machen die Verbesserungsprojekte, die sind gut. Aber das restliche Zeug, das werden wir schon irgendwie positiv berichten.” Irgendwann habe ich gesagt, wir müssen uns mal mit dem Führungsteam hinsetzen und ich zeige mal alles, was der Konzern über WCM von uns erwartet. Und irgendwann haben alle gemerkt, dass der Konzern das wirklich ernst meint. Aber als Stabsstelle bist du erst mal anderthalb Jahre am rühren und versuchst irgendwie etwas voranzutreiben. Deswegen war das nicht gut gemacht. Man hätte die Werksleiter als allererstes und intensiver einbinden müssen.
Hattet ihr zu dem Zeitpunkt schon Industrie 4.0 Ideen?
Den Begriff Industrie 4.0 gab es damals noch nicht. Ich kannte den damals jedenfalls noch nicht und habe ihn erst sechs oder sieben Jahre später zum ersten Mal gehört.
Was hast du nach dem WCM Black Belt Projekt gemacht? Wann bist du in die Produktion eingestiegen?
Ja, also, der WCM Black Belt war für mich eine ziemlich gute Vorbereitung, um dann Produktionsverantwortung zu übernehmen. Weil du danach ziemlich genau weißt, wenn ich eine Produktionslinie bekomme, wie gehe ich vor, um diese zu verbessern? Also in der Produktionslinie hast du deinen OEE, du hast dein Ausbringen und du hast deine Produktivität. Arbeitssicherheit ist natürlich immer das Wichtigste gewesen. Aber mit dieser Ausbildung hast du dann relativ gute Werkzeuge an die Hand bekommen um zu sagen okay: ich weiß jetzt ganz genau, wie ich das Thema OEE-Optimierung angehen kann, wie ich das Thema Qualität angehen kann, wie ich das Thema Arbeitssicherheit angehen kann, wie ich mit Beständen umgehen kann, usw. Und deswegen war das der perfekte Schritt, von dieser Ausbildung in die Produktionsverantwortung zu gehen. Zuerst hatte ich die Verantwortung für eine Produktionslinie und wir hatten insgesamt in dem Werk zu diesem Zeitpunkt vier Produktionslinien. Das habe ich dann ungefähr drei Jahre gemacht. Dann habe ich zu der einen noch zwei Produktionslinien hinzu bekommen. 2013 bin ich dann nach Berlin gegangen. Dort war ich dann Werkleiter von einem sehr kleinen Werk, das zwar nur eine Linie hatte, wo ich aber die Gesamtverantwortung hatte. Dort hatte ich dreieinhalb sehr interessante und lehrreiche Jahre, bevor ich dann zurück nach Stolberg kam und dort die Werkleitung übernehmen durfte.
Und was sind deine Aufgaben in der Leitung gewesen? Und was war das für eine Produktion?
Also erstmal als Linienverantwortlicher hast du die Verantwortung für den OEE und das Ausbringen von deiner Linie und natürlich für die Arbeitssicherheit an der Linie. Dadurch hast du sehr viel Daily Business. Was hatten wir gestern für Ausbringenszahlen? Was haben wir für Verluste gehabt? Und ist das wieder unter Kontrolle oder nicht? Das heißt, sehr viel unmittelbare Fehlersuche und Verbesserung. Um ein typisches Beispiel zu nennen: Die Windschutzscheibe ist ja ein Laminat und wir hatten ein Kalendrierverfahren. Dieses Verfahren war aber anfällig für einen bestimmten Fehlertyp, Randbläschen. Das heißt, im Randbereich der Scheibe entstehen kleine Luftbläschen im Laminat. Den Fehler kannst du aber nicht sofort sehen, sondern die Scheiben müssen zunächst den Autoklavprozess durchlaufen. Der dauert ungefähr eine halbe Schicht und wird in einem Batch von mehreren hundert Scheiben gefahren. Irgendwann gehen deine Scheiben dann in die Endbearbeitung und dort findet erst die Kontrolle statt. Somit hast du ein richtiges Ergebnis erst, wenn die Scheiben alle einzeln durch die Endabnahme gegangen sind. Dort wird jede Scheibe einzeln begutachtet. Da kam es ganz oft vor, dass ich nachts angerufen wurde: ja, sorry, aber wir haben gerade 20% Blasen und wissen nicht weiter. Was sollen wir machen? Sollen wir aufhören oder sollen wir weiter produzieren? Da bin ich dann oft nachts ins Werk gefahren, um mir vor Ort ein Bild zu machen. Und dann brauchst du erstmal eine Stunde oder zwei, bis du herausfindest, was der aktuelle Status ist. Haben wir in den frisch autoklavierten Scheiben immer noch diesen hohen Anteil oder nicht?
Gewisse Qualitätsverluste hast du also in deiner Produktion mit drin!?
Ja, ich habe noch keinen Produktionsprozess gesehen, der dauerhaft zu 100% fehlerfrei fertigt. Wobei es für die Blasen noch einen Nacharbeitsprozess gab, mit dem man noch einen großen Teil der Scheiben retten konnte. Mal angenommen 20% deiner Scheiben haben Blasen, dann konnte man diese 20 % aussortieren und einem Zusatzprozess unterziehen, bei dem du dann noch mal so 80%, manchmal 90% wieder gut bekommst. Wenn du Pech hast, bleiben alle schlecht und du musst sie verschrotten. Das verursacht dann weitere Herausforderungen. Haben wir noch genügend Scheiben dieser Sorte im Lager? Droht irgendwo eine Unterversorgung des Kunden? Wenn wir jetzt weiterfahren und wir bleiben bei 20%, wie viel Ausschuss habe ich dann insgesamt? Wie viel Nacharbeit habe ich? Habe ich überhaupt genug Personal um die Nacharbeit durchzuführen? Haben wir genügend Lagerfläche für die Nacharbeit? Erzeugen wir einen Engpass bei den Autoklavgestellen?
In der Regel haben wir uns dann erstmal genau angesehen, wo sich die Blasen befinden. Haben wir irgendwo einen Schwerpunkt? Sind die immer an einer Stelle oder sind sie verteilt? Befinden die sich an der Dachkante oder an der Motorkante? Dann haben wir uns natürlich die Prozessschritte angesehen, die einen Einfluss auf diese Stellen nehmen, Thesen über die möglichen Ursachen aufgestellt und 2 oder 3 Versuchsbatches zum Beispiel mit angepassten Parametern oder neuen Werkzeugen produziert. Du konntest aber nicht sofort sehen, ob es besser ist.
Dann musst du erstmal eine halbe Schicht produzieren. Und du musst sicherstellen, dass du die Anlagenbediener ran holst und ihnen ganz klar erklärst, was du gerne machen möchtest, weil der gesamte Ablauf sich über eine Schicht zieht und du ja in der Regel nicht selber bis zum nächsten Tag vor Ort bleiben kannst. Wir machen dann beispielsweise erstmal zwei Gestelle ohne Änderung, dann machen wir Änderung A und produzieren damit weitere zwei Gestelle. Die müssen entsprechend markiert werden. Dann kommen diese vier Gestelle in den Autoklav und haben Vorrang vor allen anderen Gestellen, damit du möglichst schnell ein Ergebnis zu Versuch A versus aktueller Produktion bekommst. Sobald der Autoklav aufgeht, soll jemand mit der Taschenlampe prüfen, ob es eine Verbesserung gibt und dafür sorgen, dass die Versuchsscheiben möglichst schnell über die Endkontrolllinie gefahren werden. Mit viel Glück hat man dann ein erstes und valides Ergebnis, wenn man am nächsten Morgen zurück ins Werk kommt. Das ist so ein typisches Beispiel für eine ad hoc Situation.
Was war das für eine Produktion?
Wir hatten eine nahezu voll automatisierte Produktion. Floatgläser wurden am Eingang einzeln in die Linie gelegt und durch die Linie getaktet bis sie als vorlaminierte Windschutzscheiben hinten raus kamen. Darauf folgte der bereits erwähnte Autoklavprozess, der in Batches von mehreren hundert Scheiben gefahren wurde. Den Autoklav kann man sich wie ein am Ende verschlossenes, großes Rohr mit 2m Durchmesser vorstellen, in das die Scheiben reinkommen. Dann wird der Eingang mit einem Deckel verschlossen und es wird etwa 12 bis 15 bar Druck und deutlich über 100°C Temperatur aufgebaut. Übrigens auch ein gutes Beispiel für ein Ergebnis aus einem WCM Projekt. Da haben wir Wege gefunden, mit weniger Temperatur einen stabilen Autoklavprozess zu erreichen, so dass wir Energie sparen konnten.
Nach dem Autoklavprozess kam noch die Endbearbeitung. Da wurden noch Kunststoffüberstände weggeschliffen, die Scheiben gesäubert und die Qualität kontrolliert. Dabei fährt die Scheibe unter anderem durch eine Kamera-Schranke in der geprüft wird, dass aus Fahrerperspektive keine optischen Verzerrungen außerhalb der vorgegebenen Kundentoleranzen vorliegen.
Welche Losgrößen hattet ihr?
Das war recht unterschiedlich. Wir hatten zum Beispiel den VW Golf, der in sehr großer Stückzahl gefertigt wurde. Das war zwar eine sehr anspruchsvolle Scheibe, aber das waren so große Mengen, dass du die auch schon mal fünf Tage am Stück gefahren bist. Dann fallen die Anfahrverluste nicht so sehr ins Gewicht. Es gab aber auch Modelle, die wir in seltenen und dann auch nur recht kurzen Kampagnen produziert haben. Im Schnitt hatten wir etwa alle 2,5 Tage einen Modellwechsel.
Was war eure Produktionssteuerung?
Wir hatten teilweise Kanban Systeme für Anbauteile an den Linien. Unser wichtigstes Vorprodukt war das Floatglas, von dem wir in der Regel das Glas für die aktuelle Kampagne und mindestens einen Teil der nächsten Kampagne an der Linie stehen hatten, falls wir aus irgendeinem Grund mal vorzeitig einen Modellwechsel durchführen mussten. Das Glas bekamen wir immer von Saint-Gobain Glas, teils aus dem Floatwerk, mit dem wir uns das Werksgelände in Stolberg geteilt haben, teils aus anderen Floatanlagen. Bei der Folie war es so, dass wir eine Produktionslinie hatten, die die Folie vorbereitet hat. Wir haben die Folie auf Rollen vom Lieferanten bezogen. Aber du möchtest ja wenig Verschnitt haben, deswegen ziehst du sie auf diese typische Windschutzscheibenform. Dadurch wird sie an der Motorkante dünner als an der Dachkante. Man muss natürlich auch gucken, dass alle Qualitätsanforderungen noch erfüllt sind. Für dieses “Recken” der Folie hatten wir eine eigene Produktionslinie.
Das heißt, wenn ihr eine Losgröße von XY hattet für zwei Tage, dann hattet ihr aber vorher schon die Teile angeliefert. Also unten im Keller für genau diese Losung.
Ja, oder wir haben auch teilweise die Produktion der Folien so getimed, wie wir es hinterher in der Produktion der Windschutzscheibe gebraucht haben. Das Laminieren der Folien war beispielsweise in einem Reinraum. Die Windschutzscheiben sind also in den Reinraum reingefahren, wurden laminiert und sind dann wieder rausgefahren. Und da hast du gerade in dem Reinraum nur begrenzte Lagerkapazität für Folien. Das heißt, du musstest schon sehr genau planen, welche Folien machst du wann. Du musstest auch sicherstellen, dass die Folien möglichst in einer Kampagne aufgebraucht wurden, damit sie nicht auf Dauer Lagerkapazität im Reinraum belegen. Größere Probleme, bei denen wir die Kampagne abbrechen mussten, haben dann direkt einen Rattenschwanz an Problemen mitgezogen, weil die ganzen Folien noch da liegen und du eventuell keinen ausreichenden Platz für die Folien des nächsten Modells hattest. Die Folien mussten nach dem Recken übrigens auch noch für eine Mindestdauer im Reinraum gelagert werden, weil sie sich nach dem Recken auch wieder etwas zusammenziehen und erst dann verwendet werden können.
Also gerade das mit der Folie ist ja ein gutes Beispiel für die Herausforderung einer Produktionssteuerung.
Wir hatten eine Produktionsplanung und Steuerung als Abteilung und die haben das alles geplant. Anfangs hatten wir Planer für die einzelnen Linien, später einen für alle Linien. Das wurde über SAP R3 geplant.
Das ist ja nicht ganz so leicht, alles auftragsbezogen und aufeinander abzustimmen.
Ja genau. Das war auch so eine Sache, wenn du dann irgendwie Nachts eine Entscheidung treffen musstest, dann musstest du erstmal gucken, ob du irgendwie an die Informationen kommst. Also teilweise habe ich dann da gestanden und musste entscheiden, stoppen oder nicht? Aber du weißt dann erstmal gar nicht, bekommen wir ein Problem mit der Folie, wenn wir das jetzt stoppen. Bekommen wir ein Problem mit Glas? Bekommen wir ein Problem mit Anbauteilen?
Und was für ein Produkt an Glas war das, kannst du das nochmal etwas erklären bitte!?
Eine normale Scheibe, also eine Seitenscheibe beispielsweise, wird vorgespannt, indem die heiß gemacht wird, etwa 600 Grad. Danach wird dann Raumluft in großer Menge auf die heiße Scheibe geblasen. Dabei passiert folgendes: Das Glas hat einen gewissen Wärmeausdehnungskoeffizienten. Jetzt kommt die Raumluft von außen drauf. Die Hülle wird schlagartig kälter, zieht sich ein bisschen zusammen und wird hart, während der Rest des Glases noch leicht viskos ist. Der Kern kühlt dann langsam aus. Wenn der Kern auskühlt, zieht er sich auch zusammen, ist aber schon in einer starren Hülle. So entstehen Zug- und Druckspannungen in dem Glas. Das macht das Glas stabiler und erzeugt den Sekurit-Effekt. Das heißt, wenn du es kaputt schlägst, bröselt es in ganz viele kleine Krümel und du hast nicht die Gefahr, dass dir ein Glasspieß in den Hals knallt oder sowas. Man nennt das Einscheibensicherheitsglas oder auch ESG.
Das ist wahrscheinlich auch eine Auflage!?
Ja, klar. Jedes Autoglas ist entweder laminiert, das nennt man Verbundsicherheitsglas oder auch VSG oder es ist aus ESG. Also die Windschutzscheibe muss immer laminiertes Glas sein, weil die darf nicht zerbröseln und wegfallen, sonst würde der Fahrer auch nichts mehr sehen. Das Glas muss große Splitter erzeugen, aber die müssen im Fall eines Bruches an der Folie kleben bleiben. Dann gibt es noch Gorillaglas, das wird chemisch in einem speziellen Bad vorgespannt. Dadurch kann man selbst extrem dünnes Glas mit sehr großer Vorspannung produzieren. So kannst du ganz dünnes, biegsames, aber stabiles Glas machen. Smartphone Displays bestehen daraus. In Fahrzeugverglasung wird es meines Wissens aber nicht eingesetzt.
Und was ist dann passiert in Stolberg? Wie ist es weitergegangen?
Ja, dann kam Covid. Ich glaube, VW waren die ersten, die auf 100 % Kurzarbeit, also kompletten Produktionsstopp gegangen sind. Innerhalb von 24 Stunden sind dann BMW und Mercedes gefolgt. Das heißt, unsere Kunden sind innerhalb von ein bis zwei Tagen alle auf 100% Kurzarbeit gegangen und wir dann unmittelbar auch. Wir waren für eine oder zwei Wochen in Kurzarbeit, also kompletter Produktionsstopp und alle Mitarbeiter zu Hause. Es war vorher undenkbar, dass sowas passieren würde.
Das ist ja eigentlich unfassbar!
Ja, es stand vorher immer im Raum, dass wenn wir den Kunden zu einem Bandstopp zwingen, weil wir keine Windschutzscheiben liefern, dass man uns dafür pro Stunde einen extrem hohen Betrag in Rechnung stellen würde.
Aber jetzt waren wir in Kurzarbeit. Und dann rief mich unser Geschäftsführer an und sagte: Raphael, wir gehen davon aus, dass Covid unsere Kunden noch einige Monate stoppen oder zumindest deren Produktion enorm drosseln wird. Wir gehen außerdem davon aus, dass der Markt danach sehr langsam wieder anziehen wird. Und wir nutzen jetzt die Zeit. Wir gehen bitte sofort in VK, also Produktion 24/7. Wo wir die Scheiben hinstellen, wissen wir noch nicht. Lass dir was einfallen. Stell sicher, dass wir keine Serienfehler drin haben, weil wir danach die Linie abbauen werden. Wir haben dann fünf Monate Zeit, die Linie in Herzogenrath wieder aufzubauen. Unter normalen Umständen wäre es nie möglich gewesen, eine Linie ab- und wieder aufzubauen, weil einfach die Kapazität nie ausgereicht hätte, den Auf- und Abbau zu überbrücken. Man hätte immer eine neue Linie bauen und in Betrieb nehmen müssen, bevor die andere abgebaut werden kann, weil sonst einfach die Kundenbelieferung nicht gewährleistet ist.
So wurde dann kurzerhand die Schließung bzw. Verlagerung des Werkes entschieden. Und das gerade zwei oder drei Monate nachdem wir Investitionen in Millionenhöhe für die Fertigung eines neuen Scheibenmodells mit besonderen Anforderungen erhalten haben. Ein Modell mit Augmented Reality Head up Display und Silberbeschichtung. Dann, wenige Tage nach der Entscheidung für die Verlagerung, haben wir erstmal die Mitarbeiter informiert und die Produktion wieder auf Volllast gestellt. Zum Ende mussten wir dann noch eine Woche länger produzieren als geplant. Tatsächlich eine ganz wilde Zeit. Danach wurden die Anlagen abgebaut, die Hallen aufgeräumt und wir mussten noch die ein oder andere Sonderaktion organisieren, bis das Werk dann endgültig leer war und abgeschlossen wurde. Das war meine letzte Aufgabe bei Saint-Gobain.
Und dann hatte ich diese super günstige Lage, dass ich wirklich Zeit hatte, mir Gedanken zu machen, was ich als nächstes machen will? Und so bin ich zu umlaut gekommen.
Warum bist du dann zu umlaut gegangen?
Ich bin zu umlaut gegangen, weil ich das ganze Thema Industrie 4.0 fundiert kennenlernen wollte. Ich wollte jetzt viel tiefer in die Technik rein. Ich habe zwar Elektrotechnik studiert, ich habe aber nie wirklich in und mit der Elektrotechnik gearbeitet, außer in meiner Anfangszeit bei Sekurit. Das wollte ich jetzt aufgreifen und hatte da total Bock drauf. Habe ich auch immer noch, aber das war zu diesem Zeitpunkt meine Intention, bei umlaut in diese Thematik rein zu gehen. Ich konnte mir auch das Beratungsgeschäft gut vorstellen, obwohl ich das ursprünglich mal ausgeschlossen hatte. Und weil ich jetzt etwas Zeit hatte, habe ich intensiv geschaut, was ich wirklich machen will. Dafür habe ich mir dann auch eine professionelle Coachin geholt. Und irgendwann sagte ich dann: “Ich traue es mich kaum auszusprechen, aber ich könnte mir vorstellen, in die Beratung zu gehen.” Da fing sie an zu lachen und meinte, dass sie das auch so sieht. Aber nicht irgendeine Beratung, sondern sie hat mir empfohlen, einen Blick auf umlaut zu werfen. Das habe ich getan und es hat mich direkt getriggert. Klar, die hatten ja auch ein sehr cooles Marketing bei umlaut, zumindest zu diesem Zeitpunkt und das hat mich total gecatcht. Ich habe mich dann initiativ beworben und obwohl es lukrativere Optionen gab, habe ich mich riesig gefreut, dass es geklappt hat.
Und was hast du dann bei umlaut gemacht?
Das erste Projekt war im Defense Bereich. Das fiel eher in die Art von Beratung, die ich eigentlich nicht machen wollte. Das zweite Projekt war richtig cool. Das war bei einem skandinavischen Batteriehersteller und beinhaltete das Design von MES und SCADA für eine Greenfield Fabrik. Welche potenziellen Lieferanten brauchen wir für das Projekt? Für welche Funktionen benötigen wir eigentlich das MES? Welche Zwecke soll das SCADA System erfüllen? Dabei habe ich den ganzen Batterie-Produktionsprozess ein bisschen kennengelernt.
Hattest du vorher in deiner Produktion schon mit MES und SCADA zu tun?
Ja, im Grunde hatten wir MES und SCADA Systeme und damit habe ich 15 Jahre gearbeitet. Jedoch nicht mit den neuesten Systemen. Ich wusste auch gar nicht, dass es MES und SCADA heißt. Also den Begriff MES musste ich googeln und dann habe ich gemerkt, dass das im Grunde das ist, womit ich in der Produktion zuvor gearbeitet habe. Also MES ist ja ganz viel rund um das Thema: Ermittlung von OEE, Buchung von Ausfallzeiten und vieles, was dich in deiner Produktion unterstützt. Das Projekt war eigentlich ein totaler Glücksfall, weil ich konnte da rein und die ganzen Themen lernen. Ich konnte mich sehr viel informieren rund um das Thema MES und SCADA, IT Architektur, OPC UA, die Automatisierungspyramide usw. Das war für mich toll und für den Kunden war meine Erfahrung aus der Produktion sehr wertvoll, sodass ich mich super einbringen und helfen konnte. Deswegen war das ein totales Win-Win.
Würdest du sagen, dass du als Berater praktische Erfahrung benötigst, um wirklich beraten zu können?
Das hängt von den Themen ab. Aber in dem, was ich jetzt gemacht habe: Ja! Aber du kannst ja auch als Berater praktische Erfahrung sammeln. Also es ist einerseits ein Vorteil, wenn man wie bei mir über Jahre wirklich verantwortlich Produktionsarbeit gemacht hat und die Probleme genau kennt. Was ist das Problem, wenn ich Dinge nicht vernetzt habe? Was ist das Problem, wenn mir Daten fehlen? Was bedeutet das, wenn ich die Daten nicht richtig zuordnen kann oder wenn ich diese nicht rechtzeitig habe? Was hat das für Auswirkungen? Auf der anderen Seite ist es natürlich auch ein Vorteil, wenn man irgendwie in fünf, sechs, sieben Unternehmen nacheinander reingeschnuppert hat und gesehen hat, wie haben die das gemacht? Das hatte ich ja vorher nicht.
Hattest du auch Touchpoints mit Industrie 4.0 Technologien gemacht? Also IIoT, Track and Trace, Robotics, Digital Twin usw. Also hast du damit Erfahrungen gemacht?
Ja, die ersten Erfahrungen habe ich schon bei Sekurit gemacht. Dort haben wir ein Projekt gehabt, das ein super Beispiel dafür ist. Wir bekamen den Auftrag, die Windschutzscheiben für ein neues Fahrzeugmodell zu fertigen. Die Toleranzvorgaben für diese Scheibe waren sehr viel geringer als bis dato üblich, weil das Auto ein Augmented Reality HUD (Head-Up-Diusplay) hatte. Das heißt, der Fahrer bekommt Informationen in die Windschutzscheibe projiziert. Es gibt einen Beamer hinter dem Lenkrad und dessen Bild spiegelt sich in der Windschutzscheibe. So kann man virtuelle Informationen in das reale Blickfeld des Fahrers bringen. Wenn jetzt die Scheibe nicht sehr genau gebogen ist, dann sagt dir das System möglicherweise: Pass auf, dieses Auto bremst, aber in Wahrheit bremst das Auto daneben. Deswegen waren die Anforderungen an die Scheibe sehr viel höher als bei anderen Modellen.
Windschutzscheiben werden zuerst gebogen, dann werden sie laminiert und die genaue, finale Geometrie kann erst ganz am Ende bei der Endbearbeitung, also nach dem Autoklavieren, gemessen werden. Wir haben dann Produktionsdaten gesammelt. Das heißt, wir haben zusätzliche Sensoren in den Prozess eingebaut und zudem erstmalig Wege gefunden, die während der Produktion erfassten Prozessparameter aus den Schneid-, Schleif-, Siebdruck-, Ofen- und Laminierprozessen mit den finalen Messergebnissen der jeweiligen Scheiben in Verbindung zu bringen.
So konnten wir ein Machine Learning Modell erstellen, mit dem wir bereits während der ersten Prozessschritte anhand der erfassten Parameter der einzelnen Scheibe die finale Geometrie der Scheibe mit einer gewissen Wahrscheinlichkeit vorhersagen konnten. Und diese Information haben wir dann für ein korrigierendes Fine-Tuning bestimmter Parameter im restlichen Prozess in Echtzeit genutzt, um so die geforderten Biegetoleranzen einhalten zu können. So etwas verbinde ich mit Industrie 4.0.
Wir hatten in Herzogenrath auch ein Forschungszentrum mit einem Industrie 4.0 Team.
Letzte Frage: Industrie 4.0, ist das die Zukunft für produzierende Firmen?
Ja, ich glaube schon. Es gibt ja extrem unterschiedliche Arten der Produktion. Bei Sekurit haben wir auch schon gemerkt, dass die Konkurrenz aus Polen oder Tschechien riesig war. Aber die Lohnkosten dort steigen auch und dort gab es große Schwierigkeiten, Leute für die Produktion zu bekommen. Die haben jede Menge Mitarbeiter aus Rumänien rekrutiert.
Aber wenn wir grundsätzlich mit Ländern wie Polen, Tschechien oder China und deren Preisen konkurrieren wollen, dann muss man die Automatisierung und Industrie 4.0 hier in Deutschland vorantreiben. Ich glaube, dass man beispielsweise über das Machine Learning Modell, das ich erklärt habe, die Optimierung der Produktion von einzelnen Produkten sehr gut verbessern kann. Das sollte man verfolgen, das halte ich für ganz wichtig.
Das heißt, der Treiber für Industrie 4.0 ist die Konkurrenz gegenüber anderen Produktionsstandorten in anderen Ländern?
Ja, einerseits. Andererseits kriegt man natürlich auch mit, dass das Problem mit dem Fachkräftemangel, also dem Mitarbeitermangel, immer größer wird.
Wir haben die letzten Jahre bei Sekurit in Stolberg nicht mehr ausgebildet, weil wir einfach nicht mehr genügend geeignete Bewerbungen bekamen. Und auch hier kann Industrie 4.0 große Abhilfe schaffen.
Das sind interessante Ansätze! Ich habe auch noch eine Idee, warum Industrie 4.0 eine gute Idee für Deutschland sein könnte. Und dabei spreche ich von der sogenannten VUCA Welt, also einer Welt, in der der Markt immer komplexer, immer undurchsichtiger, immer unvorhersehbarer wird. Und der Kunde will immer individualisiertere Produkte haben. Das ist doch auch ein großer Treiber oder nicht?
Aber das von dir angesprochene Problem mit der Konkurrenz gegenüber anderen Standorten in anderen Ländern leuchtet mir auch vollkommen ein. Und auch das Problem des Fachkräftemangel ist natürlich auch ein Treiber.
Und wir sprechen ja hier nur von der Automobilindustrie, die ist ja nochmal speziell. Aber du hast ja auch ganz andere Industrien.
Das stimmt natürlich auch! Produktion ist ja auch nicht gleich Produktion. Das ist ja komplett vielfältig. Also die eine Produktion kannst du nicht mit einer anderen Produktion vergleichen.
Ja, alleine schon die Montageproduktion im Automobilwerk kannst du gar nicht vergleichen mit der Produktion einer Windschutzscheibe. Und die kannst du wiederum nicht vergleichen mit der Produktion von beispielsweise Lebensmittelfarbe.
Letzte Frage: Produktionsnetzwerke, virtuelle Fabriken. Ist das das Nonplusultra der Industrie 4.0?
Mit dem Thema habe ich mich nicht intensiv auseinandergesetzt. Aber am meisten leuchtet mir das ein, wenn du Werke konzipierst. Die Herstellung von Produktionswerken sozusagen. Wenn du ein Werk konzipierst, dass du dann an mehreren Standorten bauen möchtest. Oder wenn Werke umgebaut werden. Ich habe mehrere Verlagerungen von Produktionslinien hautnah miterlebt und war als Werkleiter für die Inbetriebnahme von verlagerten Anlagen mit verantwortlich. Da war selbst bei guter herkömmlicher Planung viel Trial & Error bei der Inbetriebnahme dabei. Man muss am Anfang ziemlich kämpfen, um die Produktionsprozesse in Gang zu kriegen und steht dabei in aller Regel enorm unter Erfolgsdruck. Da sehe ich einen großen Nutzen von virtuellen Fabriken, in denen man die Prozesse bereits im Vorfeld simuliert und optimiert.
Ja, das ist das eine. Ich meine aber eine virtuelle Fabrik, die Agile Manufacturing als Paradebeispiel umsetzt.
Also, wir bauen ein reales Netzwerk aus einem Verbund von vielen Unternehmen aus einer ähnlichen Produktionsumgebung, um dann in einer virtuellen Fabrik agil produzieren zu können. Und je nach Kunde und Kundenauftrag kann diese virtuelle Fabrik immer wieder neu aus diesem realen Netzwerk entstehen. Und das sind immer einzelne Unternehmen, die dann genau für diesen Kunden produzieren. Und dann, wenn der Auftrag durch ist, dann entsteht wieder eine neue virtuelle Fabrik aus diesem Netzwerk. Das ist meiner Meinung wirklich Agile Manufacturing. Und dazu benötigen wir Industrie 4.0.
Ja, also da kann ich nicht so viel zu sagen, weil ich damit keine Erfahrung habe. Also das macht für mich schon Sinn. Ich kann mir vorstellen, dass da sehr sehr viel Verbesserungspotential drin steckt.
Leider kämpfen viele Unternehmen heute gegeneinander, die auch kooperieren könnten. Wenn sich Unternehmen zusammen täten und ein gemeinsames Produkt verkaufen würden, das wäre ein ganz neues Potenzial, das oft nicht betrachtet wird. Vielleicht ist es aber in anderen Bereichen auch so, dass das schon gang und gäbe ist. Das weiß ich nicht.
Also, ich habe viel gelernt in dem Gespräch. Es hat mir sehr viel Spaß gemacht. Da war sehr viel guter Inhalt dabei.
Ja, cool, das hat mir auch viel Spaß gemacht. Vielen, vielen Dank.
Metadaten
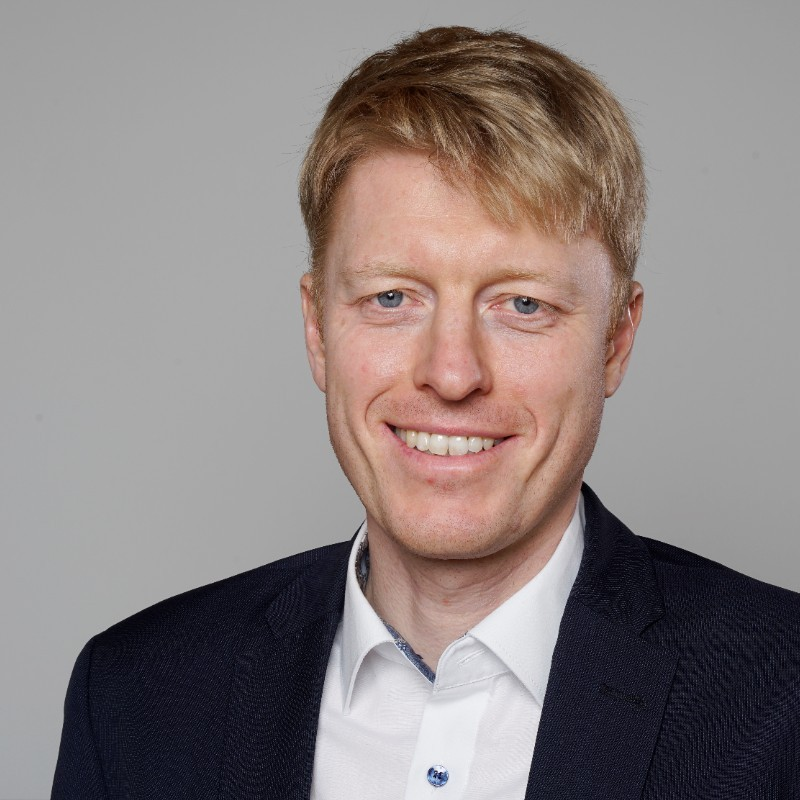
Eckdaten:
Durchführung Interview: 22.08.2024 (face to face)
Interviewsprache: deutsch
Interviewer: Stephan Bellmann
Interviewpartner: Raphael Küff
Autorisierung: 05.01.2025
Sehr interessantes Interview mit offenenm und ehrlichem Einbilick in die Prozesse der Produktion bei Segurit.